This is Part Five in Midwest Chemical Safety’s series on Leadership in Environmental Health and Safety. Catch up on the series in sequential order here:
Part One: Leaders- Not Managers In EHS Leadership
Part Two: Giving Information in EHS Leadership
Part Three: Understanding Group Needs in EHS Leadership
Part Four: Group Representation in EHS Leadership
Problem-solving
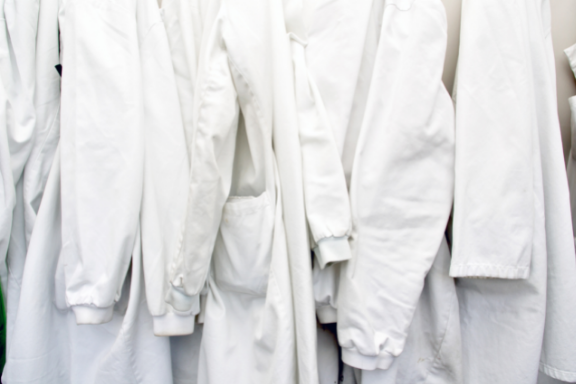
We are often faced with challenges that must be addressed and overcome. For example, using EHS-type challenges, the design and installation of a new engineered safety system at a workplace, or forming a hazardous materials emergency response team for chemical releases. Leaders need the ability to solve difficult challenges, and expertly using problem-solving skills will significantly influence the leader’s ability to get the job done and keep the group together even when faced with what seems to be an insurmountable challenge.
At its heart, problem-solving is a logical process, and there are organizations such as the American Society for Quality (www.asq.org) that have resources on problem-solving. The goal of any problem-solving methodology is to reach a solution or a decision. One process is presented below but remember that there are other processes available.
Process Flow for Problem-Solving
#1. Task consideration: Consider the following questions:
- How important/urgent is the task?
- What is the real problem? Do I understand the problem? (Consider “problem as given” vs. “problem as understood.”)
- What is the best, worst, and most likely outcome if we solve (or do not solve) this problem?
- Who owns this problem? (Is someone trying to give me their problem?) Identify all the stakeholders.
#2. Consider the resources available and what is needed
- Break down the problem into component parts.
- What are the influences sustaining and restraining the problem?
- Are there contextual or environmental limitations?
- Do you need expert advice that is not available on your team?
- Time-talent-treasure constraints.
#3. Generate solutions and alternatives
- Think “win-win” – develop consensus solutions
- Focus on agreements
- Synthesize solutions and their alternatives
- Know when to back down.
#4. Write the plan down:
- Develop a plan of action/milestones to track the solution
- Get agreement from all the stakeholders on the plan.
- Build-in on-going evaluation of the plan
- Assign resources
- Create a timetable for actions. (This is more detailed than a plan of action/milestones)
- Distribute the plan and assignments to all stakeholders.
- Implement the decision.
- Evaluate the decision
- Identify the strengths and weaknesses of the plan.
- Be flexible – implement change as necessary
- Feedforward – continuous improvement. Capture “how to make it better” ideas for the next time.
The importance of evaluating the decision cannot be overemphasized. Every decision, project, or process will have with it associated lessons learned – things that went right and things that did not go right. Capturing these “Lessons Learned’ in a file that you can refer to can be a huge time (and money) saver when faced with similar challenges.
Evaluation
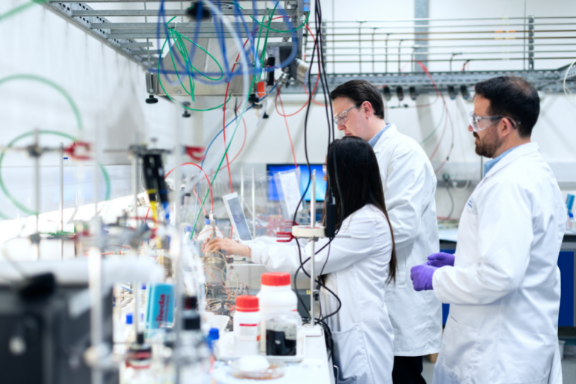
In the context of environmental, health, and safety professionals, we are continually evaluating something. Projects are evaluated against time and budget constraints; operations are evaluated against regulations; consensus standards and best management practices; and those we lead are evaluated against….what?
Leaders have an “evaluation attitude” – that is they regularly analyze for improvement, be it in a process or in performance. They also cultivate this attitude in those whom they lead. Continuous improvement cannot occur without evaluation. We do it to better ourselves, our teams, and the programs that we manage.
Things to consider: Task, Project, and Program Evaluation
Consider the following questions when evaluating tasks, projects, and programs:
- Did the final product fall short, meet, or exceed our expectations?
- Was it done on time and in budget?
- Did we choose the right path to the final product?
- Did we accurately assess risk?
- Did we fully utilize our resources? Were there any resources that we didn’t have?
- What did we like most (and least) about the task?
For evaluating a team, consider the following:
- Was everyone involved? Did everyone have a meaningful role in the task?
- What do group members think about their individual contributions?
- Is everyone happy with their own performance?
- Did the group work well together?
- Was communication clear? (If not, the leader needs to critically analyze their own communication to the group. If your team did not understand you – that is on you, not them!)
- Have weak skills been strengthened through the task? (Was there opportunity to strengthen weak skills?)
Things to Consider: Evaluating Individual Team Members
Leaders place a high value on the individual worth of every team member, understanding everyone needs to experience success in order to grow. The best evaluation is one where an individual is compared against personal standards and not those of some “universal” such as “average” or “best.”
Likewise, individuals should never be evaluated against a metric that is outside of their control. For example: a bench chemist should not be evaluated on the number of samples completed per some arbitrarily chosen time period (e.g., number of lead samples per quarter). What happens if the laboratory doesn’t receive any lead samples in a quarter? The number would be “zero” and an unfair detractor to the analyst’s performance!
Goals and Objectives
A “goal” is a general statement identifying a mid-to-long term purpose. It is normally accomplished because of completing several objectives that are much more clearly defined. The key is to create realistic goals and formulate concrete, well-defined objectives to accomplish that goal. Objectives must be measurable so that progress to the goal can be evaluated.
A well-written objective contains four parts:
- Who is acting: Usually this is the team member.
- What is being done: Use positive, measurable actions. Stay away from phrases like “be familiar with” or “to appreciate” or “grasp the significance of”
- How often it will be done.
- How well it must be done. This, too, should be objective and measurable.
Objectives can be tested using the SMART criteria:
S – Significance. Does the objective have significance to the team and to the individual? Will it have an overall impact?
M – Measurable. Can it be objectively measured? Can progress be tracked?
A – Appropriate. Is the objective within the job responsibilities?
R – Realistic. Can it be accomplished or brought to a successful conclusion? Does the individual have control over the objective?
T – Timely: Can the objective be accomplished in the allowed time?
Ideally, both the team member and the team leader will formulate goals and objectives together.
Want to take your EHS Team to “Best in Class” but don’t quite know where to start? Call Midwest Chemical Safety, LLC, 217-971-6047 or contact me by email at harry@midwestchemsafety.com See the original LinkedIn Post Here.