This is Part One in Midwest Chemical Safety’s series on Normalcy After Covid-19. Read the next in the series here:
Part Two: Normalcy After Covid-19: Part Two
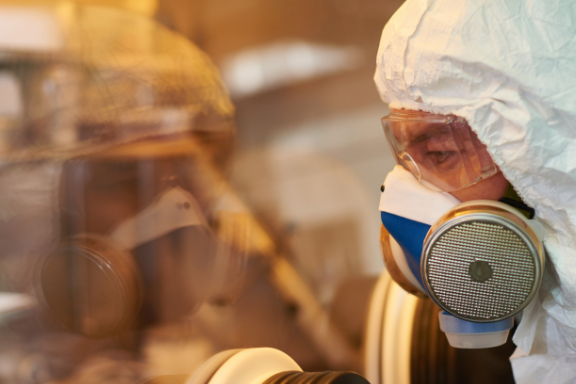
We have been at it for over six weeks now. Shutdown. Our businesses have been interrupted for a month and a half now due to Covid-19 but there is an end in sight. Many areas throughout the nation are pivoting to re-open. However, no one yet knows what new rules there may be. Many of us in the safety community believe that there will be a “new normal” with respect to how we will be conducting business. New requirements may include limited occupancy in rooms/distancing requirements or PPE requirements where none existed before. Whatever those requirements might be, there will be a new normal before we get back to business as usual.
By now we have all figured out that it’s easier to turn things off than it is to restart them. Restarting business processes is a process in and of itself. There is a logical progression from shutdown to operation. While major corporations will, have “business continuity plans” that cover many aspects of restart, most small companies, research organizations or smaller colleges/universities probably will not have such plans. If you do not have a plan in place, you need to develop it now. Hoping for the best is not a strategy that will be successful.
There should be two aspects to focus on for recovery: “People” and “things.” Take care of the people and their well-being first as you work on restarting “things.
The Harvard Business Review (https://hbr.org/2020/04/preparing-your-business-for-a-post-pandemic-world) published an excellent article on preparing your business for the post-COVID-19 activities. They looked at the five “Ps” of recovery:
- Position: This is a hard, honest assessment of your view of what the “new reality” will look like. In this assessment, decide for your business triggers that will start milestones to recovery. Examples of these triggers can be “no new cases in 14 days” or “only allow anti-body positive persons on site.” Using guidelines provided by the CDC, your business will need to decide for itself when to start activities leading to normal operations.
- Plan: Understand that what you do today will impact what is going to happen tomorrow. Your plans will need to be flexible while covering key aspects of return-to-work for the workforce and the workplace.
- Perspective: How will the work environment change as a result of the COVID-19 pandemic? It will certainly not be the same.
- Projects: While restarting an entire business such as a college campus or a small production facility may seem daunting, it becomes less so if it is broken down into smaller project-sized pieces that will, in the end, mesh together for the full facility restart.
- Preparedness: Intertwined with “projects” above, we want to be prepared for anticipated failures. For example, what if key personnel are unavailable for restart?
Planning
When it comes to recovery planning, Steven Covey said it best, “Begin with the end in mind.” (7 Habits of Highly Effective People). With that thought, what will the new normal look like? Here are some thoughts:
- Secondary schools, college and universities may have classes without face-to-face interactions for an extended period, well into the 2020-2021 school year.
- If occupancy restrictions are in place to maintain distance between people, we might see 4-person labs become 2-person labs.
- Office spaces and production floors may be at half or less occupancy.
In order to effectively plan for restart, we will need to establish productivity goals for six, 12, 18 and 24 months into the recovery. We should do our planning at the highest administrative level to be effective without being overwhelming. Effectively, those levels would be:
- For the academic community – perform planning at the college and department levels. (e.g. “College of Arts and Sciences” and “Chemistry Department” respectively).
- For the industrial community – perform planning at the operational unit level.
- For the service community – plan by logical unit organization. (e.g. A large legal firm will have plans for the “patent,” “business liability,” organizations respectively).
- For government organizations – plan by agency subunits
A complete planning hierarchy might look like this:
Information and needs will flow UP, Resources will flow DOWN.
Now that we have a plan, we need to execute it. We will discuss that in Part 2 of this series.
Midwest Chemical Safety, LLC can assist your organization with complete restart project management services. Contact Harry Elston at 217-971-6047 or harry@midwestchemsafety.com to set up an appointment. See the original LinkedIn Post Here.